Every Pile, Any Time™
Get the Answers
You Need from Stockpile Reports
How much material do you have on hand? How much material did you have yesterday? How much will you have tomorrow?
Using imagery to digitize your stockpiles to create verified Stockpile Reports so you know the volume and condition of every stockpile at any time.
What is a Stockpile Report?
Our algorithms automatically analyze imagery and identify potential risks to bulk materials estimates from measurement to measurement for precision. Every Stockpile Report includes a 3D visualization to represent the volume and condition of every pile, with a confidence score based on surface and toe calculations for each stockpile, as well as identification of risks associated with each pile, from obstructions to site conditions.
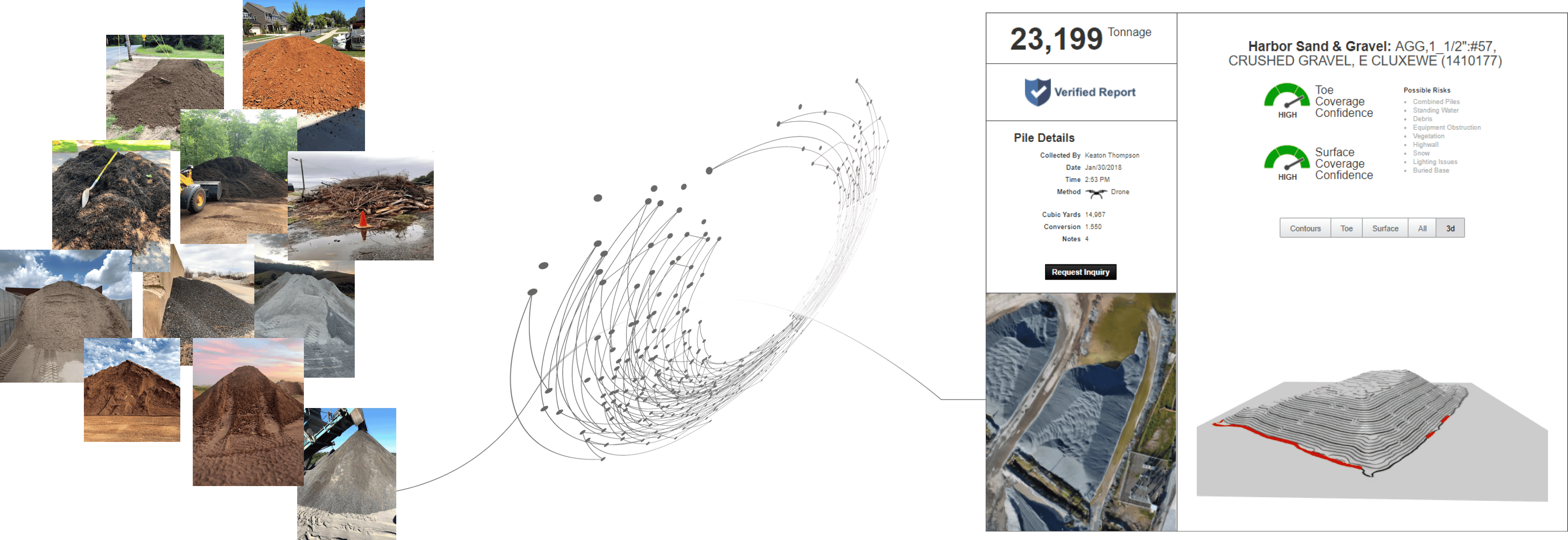
Our Plans
Personal
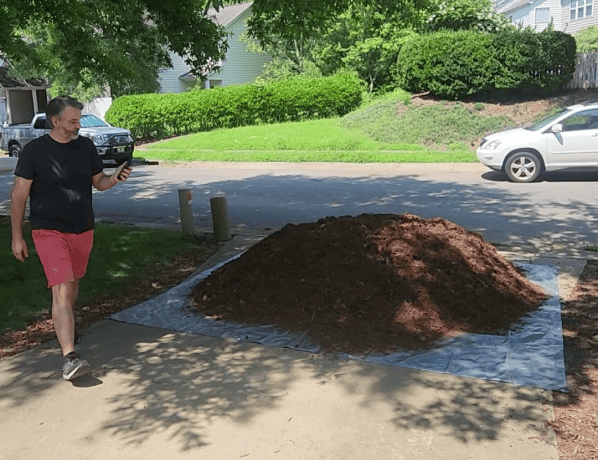
$0/ month
Are you an individual who occasionally needs a single measurement with your phone on any given day?
1 User
1 Measurement per day
Measure with an iPhone
Freestanding piles
Save measurements locally
Limited Time on Android
1 User
Unlimited measurements
Measure on a Samsung Galaxy S25
Freestanding piles
Measurements are not saved or stored
Professional
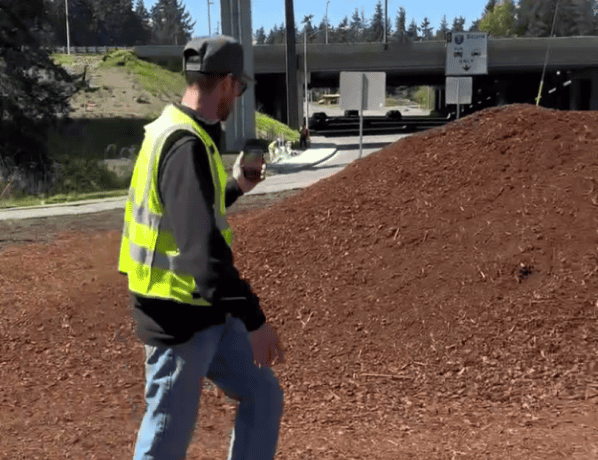
$20/ month
Are you an individual who needs 1 or more measurements of freestanding piles or materials stored in bunkers with your phone on any given day?
1 User
Unlimited measurements
Measure with an iPhone
Freestanding piles
Bunkers and bins
Save measurements locally
Business
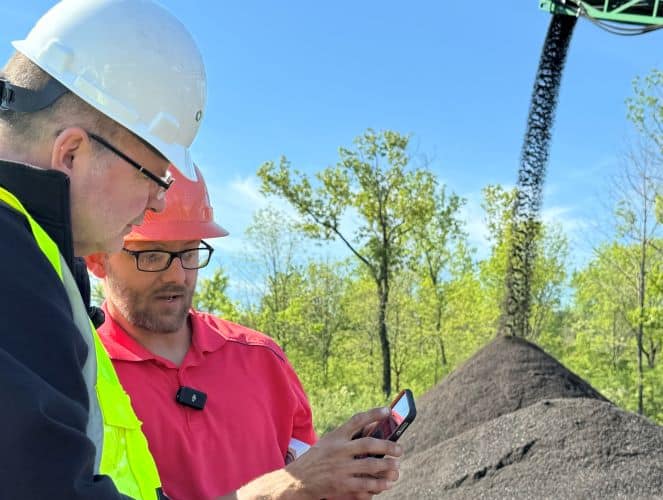
Are you a small business owner who would like a team performing unlimited measurements with their phone?
Starts at 1 user
Unlimited measurements
Measure with an iPhone
Freestanding piles
Bunkers and bins
Cloud portal and dashboard
Manage piles by product & site
Reports in tonnage
Share measurements
Enterprise
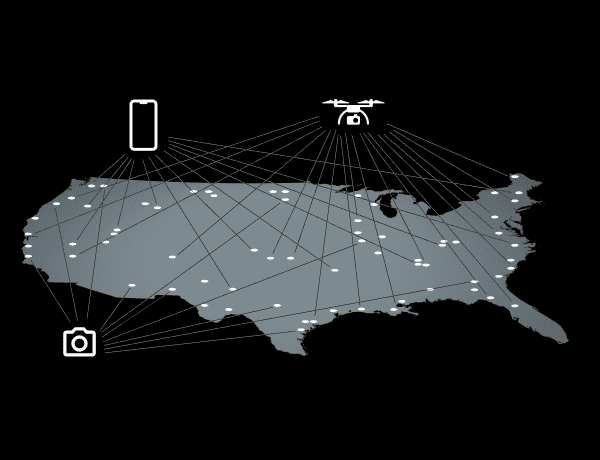
Contact Us
Are you a large enterprise with 100s of stockpiles spread across multiple states, countries, or continents that needs to conduct massive inventory counts quickly with phones, drones, and installed cameras?
Unlimited users
Unlimited measurements
Measure with an iPhone
Measure with drones
Installed cameras
Freestanding piles
Bunker and bins
Cloud processing
Cloud portal and dashboard
Manage piles by product & site
Reports in tonnage
Verified reports
Surface & toe confidence scores
Share measurements
Dispute resolution
User hierarchies
Personal
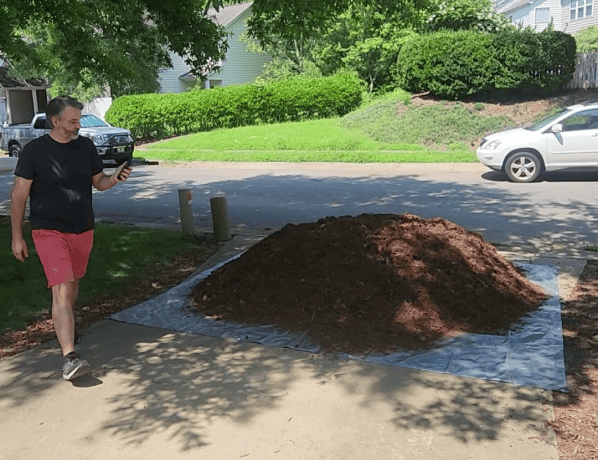
$0/ year
Are you an individual who occasionally needs a single measurement with your phone on any given day?
1 User
1 Measurement per day
Measure with an iPhone
Freestanding piles
Save measurements locally
Limited Time on Android
1 User
Unlimited measurements
Measure on a Samsung Galaxy S25
Freestanding piles
Measurements are not saved or stored
Professional
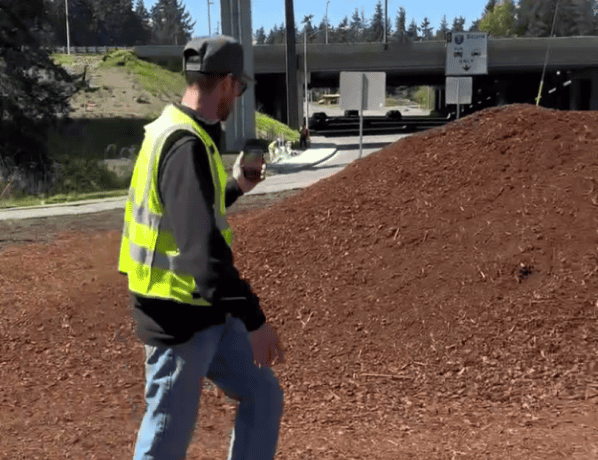
$200/ year
Are you an individual who needs 1 or more measurements of freestanding piles or materials stored in bunkers with your phone on any given day?
1 User
Unlimited measurements
Measure with an iPhone
Freestanding piles
Bunkers and bins
Save measurements locally
Business
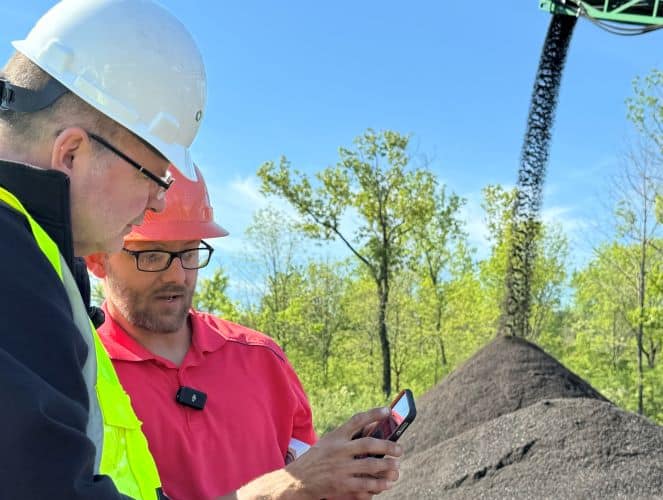
Are you a small business owner who would like a team performing unlimited measurements with their phone?
Starts at 5 users
Unlimited measurements
Measure with an iPhone
Freestanding piles
Bunkers and bins
Cloud portal and dashboard
Manage piles by product & site
Reports in tonnage
Share measurements
Enterprise
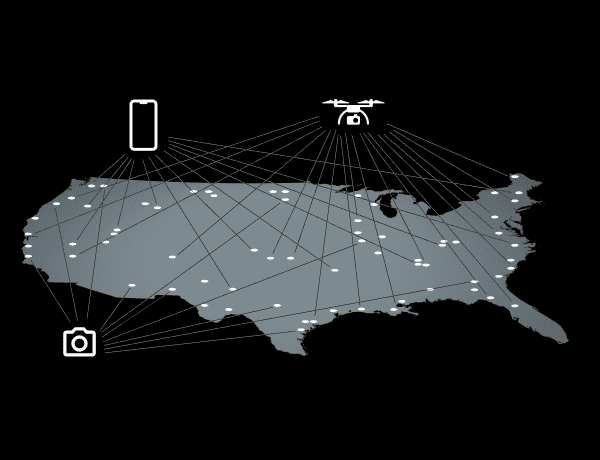
Contact Us
Are you a large enterprise with 100s of stockpiles spread across multiple states, countries, or continents that needs to conduct massive inventory counts quickly with phones, drones, and installed cameras?
Unlimited users
Unlimited measurements
Measure with an iPhone
Measure with drones
Installed cameras
Freestanding piles
Bunker and bins
Cloud processing
Cloud portal and dashboard
Manage piles by product & site
Reports in tonnage
Verified reports
Surface & toe confidence scores
Share measurements
Dispute resolution
User hierarchies
Trusted By
